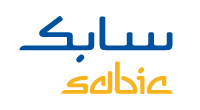
27 Oct 2010
SABIC Showcases Culture of Innovation at K 2010
Bergen op Zoom, the Netherlands – October 27, 2010 – At K 2010, Hall 6, Stand D42, SABIC is showcasing new technologies, expanded capabilities and strong customer relationships that comprise its theme for the show: Culture of Innovation. A key focus is SABIC’s sustainability strategy, underscoring the company’s commitment to addressing worldwide sustainability issues – including energy and greenhouse gas reduction, water conservation and material efficiency. The SABIC stand features an impressive array of materials from its broad and growing portfolio that enable breakthrough applications across major growth sectors such as healthcare, automotive, electronics, packaging, film and alternative energy.
“Participation at K 2010 allows SABIC to demonstrate our steadfast, long-term commitment to the plastics industry and our customers,” said Khaled Al-Mana, executive vice president, Polymers, SABIC. “Our Culture of Innovation focus drives SABIC’s strategy to be the preferred world leader in chemicals and plastics. We are proud to show how investments in our global capabilities and portfolio help us achieve mutual success with our customers.”
“SABIC is investing and driving growth in the global plastics industry by providing material solutions that deliver better performance and added value to our customers,” said Charlie Crew, president and chief executive officer, SABIC Innovative Plastics. “In keeping with our long, rich history of innovation, we continue to expand the boundaries of materials excellence with next-generation products, processing expertise, and advanced application development capabilities to help customers differentiate, compete and grow. Our number-one priority is to support our customers’ success.”
SABIC’s Culture of Innovation theme for K 2010 is built on four strategic pillars: growth, technology, sustainability and customer focus.
1. Growth
To meet customers’ requirements today and tomorrow, SABIC continues to invest in the expansion of global production capacity and to add new technology resources in key sectors.
• SABIC’s Expanded Capacity – In 2009, the company added more than one-million tons of polymer capacity at its plants in Sharq and Yansab in Saudi Arabia; expanded bi-model high-density polyethylene (HDPE) production in Germany; and opened a new low-density polyethylene (LDPE) facility in the United Kingdom (U.K.). Considerable capacity will be added when SABIC’s plants in Saudi Kayan and Al-Jubal, Saudi Arabia come online in the near future.
• SABIC® PP Compounding Capabilities – The company will add state-of-the-art specialty PP compounding to its Bay St. Louis, Miss., site in the first quarter of 2011 to satisfy demand from the North American automotive sector. The new Genk, Belgium facility, the largest greenfield PP compounding plant ever built in Europe, will supply polypropylene (PP) compounds to Europe and Stamax® composites to Europe and Asia Pacific.
• Ultem* Polyetherimide (PEI) Resin Production Facility – SABIC Innovative Plastics new Ultem PEI resin production facility in Cartagena, Spain opened in September and will provide customers with enhanced supply reliability. Further, sophisticated technology and scalable capacity for producing ultra-high-temperature Extem* resin grades and specialty intermediates (anhydrides) have been incorporated.
• LDPE Plant – SABIC's Teesside, United Kingdom, plant has a name plate capacity of 400 kt/year (which makes it the largest plant of its kind in the world). The material targets growing customer needs for packaging applications. This capacity enables SABIC to ensure a reliable and long-term supply of LDPE.
• Exatec* Plasma Coating Technology – There has been an upgrade to the SABIC Innovative Plastics’ businesses plasma coating capabilities at its United States global technology center in Wixom, Mich. The upgrade expands plasma coating capabilities for Lexan* polycarbonate (PC) glazing solutions. These enhanced plasma coatings have been shown to improve the scratch and abrasion resistance of Lexan PC glazing.
2. Technology
SABIC continues to focus on the development of new and future innovations, giving customers a broad and growing portfolio of materials technologies. These materials deliver better performance and added value by reducing system costs, opening up new design opportunities, and driving market penetration and growth. Key technologies include:
• Polyethylene Terephthalate (PET) Tape Fabric – Jointly developed by SABIC and the Austrian engineering company, Starlinger & Co. Gesellschaft m.b.H. The new fabric can be made with material input that is reduced drastically, compared with a woven fabric made from filaments, while the high-quality chemical and physical characteristics of PET are maintained.
• Extem Resin Blends – A new, incredibly tough family of high-end resin blends for electrical applications, with one of the industry’s highest continuous use heat performance meeting UL 746B requirements up to 240C.
• SABIC PP Flowpact Copolymers – Delivering measurable benefits to converters, particularly for thin-wall packaging. They offer shorter cycle times, lower energy costs and increased down gauging possibilities, and have proven successful in the high-end food packaging sector.
• Ultem PEI Composite Aerospace Board (CAB) – A superior alternative to thermoset aramid honeycomb composites, co-developed and manufactured with Crane & Co. Advantages include much faster cycle times and the ability to be “re-skinned” to lengthen its useful life.
• Light Emitting Diode (LED) Portfolio of Advanced Resin Technologies – Including flame-retardant (FR) Lexan PC resin enabling thin-wall transparent lighting and diffusion applications with UL94 V0 compliance at 1.5 mm.
• SABIC LD/LLDPE – A combined concept with multi layer film, this material enables converters of consumer packaging to reduce material usage considerably while optimizing performance on their equipment. Customers benefit from cost savings, improved down gauging opportunities, higher processing speeds, and lower energy consumption.
• Conductive Noryl GTX* 98 Polyphenylene Oxide (PPO) Resins – Allows automotive designers greater freedom to create larger top-quality, high-precision body panels than previously feasible. They cut the coefficient of thermal expansion (CTE) by 20 to 40 percent vs. previous grades for increased dimensional stability and improved gap and flush management.
3. Sustainability
Global sustainability issues are at the core of SABIC’s business strategy, built on the company’s commitment to maximize the usefulness of valuable natural resources. Customers want solutions that help reduce their environmental footprint by cutting energy consumption during manufacturing; that help reduce the weight of their products or make them thinner; and that are more easily recycled or include recycled content. SABIC’s product portfolio, technological expertise and history of innovation enable the development of materials that can help customers tackle a wide variety of environmental issues.
Sustainability examples announced here today include:
• SABIC Innovative Plastics’ Sustainability Solutions Portfolio – The company is announcing its expanded Sustainability Solutions portfolio and new validation process for sustainable materials, designed to help customers worldwide lower their carbon and energy footprints, eliminate waste, and ensure strict compliance with global environmental regulations. All products meet an appropriate third-party standard or, in the absence of a recognized standard, pass an evaluation of their environmental benefits using a rigorous Sustainable Product Scorecard developed with top environmental sustainability consulting firm, GreenOrder.
• SABIC PP Qrystal – Delivering new, improved levels of optical performance and energy savings for converters. It can be processed at significantly lower temperatures than comparable grades without any loss of transparency, delivering energy savings of as much as 15 percent.
• Post Consumer Recycled (PCR) Materials – New significantly expanded array of SABIC Innovative Plastics PCR additions to the company’s successful Valox iQ*, Xenoy iQ*, and Lexan EXL PCR product lines include Cycoloy* PCR resins, Noryl* Classico PCR resins and three new grades of Lexan EXL resins.
• SABIC Vestolen A RELY – A new standard for HDPE high-pressure pipe applications enabling converters to achieve considerable energy savings and supporting environmentally responsible trenchless pipe installation. SABIC also developed a state-of-the-art Strain Hardening test for evaluating the crack resistance behavior of HDPE pipes. This methodology avoids the use of detergents that can pose an environmental hazard.
• SABIC LDPE Ultra Melt Strength (UMS) Line – Provides the opportunity to lower the density of foam applications considerably while maintaining the same mechanical properties and improving thermal performance. This outstanding combination of properties results in noticeable material and energy savings.
• New Ultra-Stiff Lexan Thermoclear* Multi-wall PC Sheet – Has the capability to withstand wind and snow loading pressures of up to 2200 N/m2 for roofing and cladding, provides outstanding design freedom for large architectural applications such as sports stadiums. It offers exceptional stiffness, lower weight vs. glass, and two-sided ultraviolet (UV) coating for long-term durability.
4. Customer Focus
To help customers innovate, differentiate their applications, and optimize manufacture, SABIC works collaboratively throughout the application development process. A dedicated local team presence around the world enables the company to meet unique customers’ needs in a broad range of geographies and industries.
Customer innovation seminars will be held at SABIC’s booth during the course of the K show. These seminars are focused on educating and assisting customers in solving real-world challenges with SABIC materials technologies and innovations to help customers grow their businesses. Seminars range from metal replacement; reducing weight in automobiles; maximizing sustainability opportunities; and high-performance materials for the aircraft and rail markets to the use of thermoplastics in photovoltaics; innovative solutions using Lexan polycarbonate sheet; resins for the healthcare industry; and more.
The full program is available at www.sabic.com/K2010 and www.sabic-ip.com.
SABIC’s Culture of Innovation Lounge
Underscoring the theme of innovation, the SABIC stand is a unique, double-decker, 1,200 m2 (12,917 ft2) design named Culture of Innovation lounge. The stand is based on the structure of a molecule as the core building block of existence and SABIC materials were used in the construction. For example, the new grade of Lexan SG305-OB PC sheet is used for the interior and exteriors walls of the stand to illuminate the dynamic LED light band flowing along the top edge of the structure. This unique product offers both uniform light diffusion to eliminate LED “pinholes” and a view of light sources, and superior light transmission for exceptional optical brightness at lower energy costs.
SABIC is exhibiting at K’ 2010 in Düsseldorf, Germany in Hall 6, Stand D42.
For K2010 SABIC’s focus is a Culture of Innovation, which means investing in Growth, Technology, Sustainability and Customer Focus. We help our customers to innovate, differentiate their applications and optimize costs by:
• investing in global expansion,
• providing the broadest product portfolio that delivers better performance and adds value,
• developing environmentally responsible products and solutions that provide significant and measurable performance advantages,
• working closely with our customers to build long-term relationships and lasting partnerships
Reader enquiries
Innovative Plastics | Polymers | |
1 Plastics Avenue | Europaboulevard 1 | |
Pittsfield, Mass. | 6135 LD Sittard | |
United States | Netherlands | |
Tel: +1 413 448 7383 | Tel: +31 (0)46 722 2399 | |
Email: jodi.kennedy@sabic-ip.com | Fax: +31 (0)10 264 4823 | |
Web: www.sabic-ip.com | Email: rachel.kundra@sabic-europe.com | |
Web: www.sabic.com |
Netherlands
Notes for editors
About SABIC
Saudi Basic Industries Corporation (SABIC) ranks among the world’s top six petrochemical companies. The company is among the world’s market leaders in the production of polyethylene, polypropylene and other advanced thermoplastics, glycols, methanol and fertilizers.
SABIC recorded a net profit of SR 9 billion (US$ 2.4 billion) in 2009. Sales revenues for 2009 totaled SR 103 billion (US$ 27 billion). Total assets stood at SR 297 billion (US$ 79.2 billion) at the end of 2009.
SABIC’s businesses are grouped into Chemicals, Polymers, Performance Chemicals, Fertilizers, Metals and Innovative Plastics. SABIC has significant research resources with six dedicated Technology & Innovation Centers in Saudi Arabia, Europe, the USA and India. The company operates in more than 40 countries across the world with 33,000 employees worldwide.
The company has 19 world-scale complexes in Saudi Arabia. Elsewhere, SABIC manufactures on a global scale in the Americas, Europe and Asia Pacific. SABIC’s overall production has increased from 35 million metric tons in 2001 to 59 million metric tons in 2009.
Headquartered in Riyadh, SABIC was founded in 1976 when the Saudi Arabian Government decided to use the hydrocarbon gases associated with its oil production as the principal feedstock for production of chemicals, polymers and fertilizers. The Saudi Arabian Government owns 70 percent of SABIC shares with the remaining 30 percent held by private investors in Saudi Arabia and other Gulf Cooperation Council countries.
Media Notes
As an acronym, SABIC should be all caps whenever it appears in print.
® SABIC and Stamax are registered trademarks of SABIC.
* Trademarks of SABIC Innovative Plastics IP BV.
Editorial enquiries
Rachel Kundra
SABIC
Kevin Noels
Marketing Solutions NV