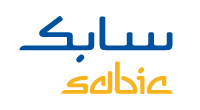
20 Sep 2010
SABIC® Vestolen A RELY Achieves New Standards for Sustainability, Performance, Cost Effectiveness in HDPE Pipe Applications
Sittard, the Netherlands – September 20, 2010 – At the Plastic Pipes XV Conference in Vancouver, Canada (stand 6) SABIC, a global plastics industry leader, today introduced the new SABIC® Vestolen A RELY family of tough, sustainable and cost-effective bimodal high-density polyethylene (HDPE) materials for pressure pipe applications. The SABIC® Vestolen A RELY portfolio offers converters considerable energy savings and enables environmentally responsible pipe installation. Further demonstrating its commitment to sustainable technologies, the company also presented today its revolutionary new Strain Hardening method, a fast, cost-efficient and highly accurate method for evaluating the slow crack growth resistance behaviour of HDPE. This Strain Hardening method avoids the use of detergents - that can pose an environmental hazard – and avoids the use of valuable drinking water.
Both announcements underscore SABIC’s increasing focus on the development of high-performance, sustainable technologies, and its ongoing investment in innovative materials and validation techniques to help converters, developers and builders leverage next-generation, pressure pipe solutions. The term “RELY” refers to the material’s outstanding reliability, which is critical for transporting potable water, gas and other valuable liquids. It also reflects SABIC’s global reputation as a strong and reliable business partner that can ensure a long-term supply of advanced material solutions.
“Our new SABIC®Vestolen A RELY products in combination with the Strain Hardening method - that measures their performance - are key deliverables in SABIC’s global strategy to supply the pressure pipe industry with breakthrough technologies,” said Jean Engels, business manager HDPE SABIC. “SABIC takes great pride in proactively developing materials and methodologies that meet current and emerging industry needs, particularly in the areas of sustainability and cost effectiveness. We also welcome new partners who can help us drive development of new pipe solutions utilizing our high-performance HDPE materials and extensive technological resources and expertise.”
Boosting Sustainability and Performance of High-Pressure Pipe
The first two grades within the SABIC® Vestolen A RELY portfolio – one designed for low sagging and the other engineered for high resistance to slow crack growth – contribute to the eco-responsible production and use of pressure pipe. With these materials, converters can significantly reduce energy. Developers and contractors can select trenchless pipe installation such as guided boring and horizontal directional drilling that reduce impact on the environment.
Both new materials are classified as PE100 grades, demonstrating compliance with the highest industry standards for HDPE pressure pipe.
• SABIC® Vestolen A RELY 5924R delivers excellent low sag performance for large-diameter pipes and pressure pipes with a low standard dimension ratio (SDR). This grade has an internal pressure approval for PE 100 that complies with the EN12201 and EN1555 standards, underscoring its high quality and outstanding performance for transporting potable water, gas, sewage and other liquids.
• SABIC® Vestolen A RELY 5922R offers excellent resistance to slow crack growth propagation in high-pressure pipe applications and can therefore be used with advanced trenchless pipe installation technologies such as re-lining, horizontal directional drilling and guided boring. Its superior resistance to slow crack growth is demonstrated by results of the FNCT (>8760h) and pipe notch test (>8760h, DIN and ISO 13479). This grade also has an internal pressure approval for PE 100, meeting EN12201 and EN1555 standards.
Moreover, the new, premium-performance RELY family is produced at SABIC’s state-of-the-art HDPE plant in Gelsenkirchen, Germany, which was designed to put less stress on the environment than traditional facilities. For example, SABIC’s plant cuts electricity usage by 8 percent, air emissions by 85 percent and sewage by 50 percent. Further, the facility uses SABIC’s own proprietary catalyst technology, ensuring a consistent and high product quality.
Setting the standard for slow crack growth resistance testing
Until now, the primary slow crack growth resistance testing methods for HDPE for pressure pipes had significant drawbacks, including high cost, long durations of a year or more and uncertain reliability. SABIC’s new and more sophisticated Strain Hardening method correlates very well to traditional methods that assess the slow crack growth behaviour of HDPE. This revolutionary method is typically able to determine the intrinsic slow crack growth behaviour via a simple tensile test at 80°C. Advantages of this test method are very low measurement variation, absence of surfactants and notches, small amount of required testing material (< 50 g) and, most important, testing times of only a few hours.
SABIC´s new Strain Hardening method can be easily implemented at accredited laboratories. This simple yet cutting-edge test fulfils an urgent and previously unmet market need. SABIC anticipates that the Strain Hardening method will become the standard for HDPE slow crack growth testing.
SABIC® Vestolen A RELY 5924R and SABIC® Vestolen A RELY 5922R are available globally. Additional grades within this product line are due for release in the near future.
SABIC is exhibiting at K’ 2010 in Düsseldorf, Germany in Hall 6, Stand D42.
For K2010 SABIC’s focus is a Culture of Innovation, which means investing in Growth, Technology, Sustainability and Customer Focus. We help our customers to innovate, differentiate their applications and optimize costs by:
• investing in global expansion,
• providing the broadest product portfolio that delivers better performance and adds value,
• developing environmentally responsible products and solutions that provide significant and measurable performance advantages,
• working closely with our customers to build long-term relationships and lasting partnerships
Reader enquiries
Innovative Plastics | Polymers | |
1 Plastics Avenue | Europaboulevard 1 | |
Pittsfield, Mass. | 6135 LD Sittard | |
United States | Netherlands | |
Tel: +1 413 448 7383 | Tel: +31 (0)46 722 2399 | |
Email: jodi.kennedy@sabic-ip.com | Fax: +31 (0)10 264 4823 | |
Web: www.sabic-ip.com | Email: rachel.kundra@sabic-europe.com | |
Web: www.sabic.com |
Netherlands
Notes for editors
About SABIC
Saudi Basic Industries Corporation (SABIC) ranks among the world’s top six petrochemical companies. The company is among the world’s market leaders in the production of polyethylene, polypropylene and other advanced thermoplastics, glycols, methanol and fertilizers.
SABIC recorded a net profit of SR 9 billion (US$ 2.4 billion) in 2009. Sales revenues for 2009 totaled SR 103 billion (US$ 27 billion). Total assets stood at SR 297 billion (US$ 79.2 billion) at the end of 2009.
SABIC’s businesses are grouped into Chemicals, Polymers, Performance Chemicals, Fertilizers, Metals and Innovative Plastics. SABIC has significant research resources with six dedicated Technology & Innovation Centers in Saudi Arabia, Europe, the USA and India. The company operates in more than 40 countries across the world with 33,000 employees worldwide.
The company has 19 world-scale complexes in Saudi Arabia. Elsewhere, SABIC manufactures on a global scale in the Americas, Europe and Asia Pacific. SABIC’s overall production has increased from 35 million metric tons in 2001 to 59 million metric tons in 2009.
Headquartered in Riyadh, SABIC was founded in 1976 when the Saudi Arabian Government decided to use the hydrocarbon gases associated with its oil production as the principal feedstock for production of chemicals, polymers and fertilizers. The Saudi Arabian Government owns 70 percent of SABIC shares with the remaining 30 percent held by private investors in Saudi Arabia and other Gulf Cooperation Council countries.
About SABIC in Europe
In Europe, SABIC has 13 world-scale production facilities which manufacture innovative plastics, polyethylenes, polypropylenes and chemical products. Throughout Europe, SABIC employs approximately 6000 people.
The main European offices for three of SABIC’s strategic business units are located in The Netherlands - Innovative Plastics (Bergen op Zoom), Polymers (Sittard) and Chemicals (Sittard). They operate an extensive network of local sales offices and logistical hubs throughout Europe which are also responsible for the sales of products manufactured elsewhere in the world.
SABIC’s European research facilities form part of the global Technology and Innovation organization and can be found in the Netherlands (Geleen and Bergen op Zoom) and Spain (Cartagena).
Media Notes
• As an acronym, SABIC should be all caps whenever it appears in print.
• ® Trademark of SABIC
Related images
Editorial enquiries
Solange Schlösser
SABIC
Brigitta de Vries
Marketing Solutions NV