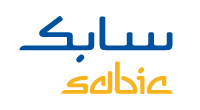
16 Oct 2012
Customers across key market segments benefit from SABIC's extensive portfolio of Innovative and Polymer solutions at the Fakuma
FRIEDRICHSHAFEN, Germany, October 16, 2012 - Customers in key markets such as Transportation, Automotive, Consumer, Packaging, Healthcare and Lighting, will see how their challenges can be met by the extensive range of thermoplastic polymers and compounds from SABIC, a world leader in polymers and engineering plastics. Addressing customer needs in Sustainability + Performance will be highlighted at the Fakuma, the international trade fair for plastics processing, in Friedrichshafen, Germany (October 16-20, 2012) at SABIC's stand 5506 in Hall B5.
Dr. Konrad Hellmann, SABIC’s Country Leader in Germany, stated: “The 21st century will pose many challenges such as how to achieve more fuel efficiency in the automotive industry and how to address water preservation and food production challenges. Delivering solutions that are tailored to local needs to help our customers meet global demand is a fundamental focus of SABIC and is achieved by combining our innovation capabilities with our uniquely comprehensive portfolio of products. Fakuma will demonstrate how many of our partners in Germany, both big and small, are champions of innovation and how, together, we are sharing success and driving growth.”
The ambitions of our customer and the growth of their business will be at the forefront of what we will show at Fakuma,” said Albert Walter, Sales Leader for SABIC’s Polymers business in Germany, Austria and Switzerland. He continued, “This is an important event to showcase our ability with product based solutions that encompass the full spectrum of engineering and thermoplastic polymers. We welcome those visitors who come to Fakuma from a wide selection of industry segments and look forward to demonstrating the range of performance materials we can offer to meet their needs.”
Customer Solutions for Public Transportation
SABIC’s Innovative Plastics business recently launched the new LEXAN™ FST3403 (flame-smoke-toxicity) polycarbonate (PC) copolymer, the first thermoplastic solution for rail seating applications to meet the strictest fire safety requirements under the CEN/TS 45545 standard. Now commercial a full two years before this European standard goes into effect, new high-performance LEXAN FST3403 copolymer – developed specifically for seat back shells and side covers – achieved the highest possible hazard level rating (HL3) under CEN/TS 45545-2 R5.
SABIC’s multi-year collaboration with GRAMMER Railway Interior GmbH is an example of its longstanding commitment to the rail industry and our proactive efforts to help customers stay ahead of increasingly stringent safety requirements. SABIC worked with GRAMMER on their development of the seating components. Importantly, the LEXAN FST copolymer can be moulded into GRAMMER’s existing tooling, avoiding significant capital costs and provides exceptionally high flow, which enables large parts to be injection moulded with high-quality aesthetics.
Customer Solutions for Automotive
Also featured at SABIC’s booth are solutions to help automakers address challenges ranging from weight reduction for improved fuel efficiency and enhanced sustainability to greater design freedom and crash and energy management.
One of the highlighted applications is a lower leg protector/undertray moulded out of SABIC’s XENOY iQ™ resin, chosen by Ford for the pedestrian safety system of its 2011 C-MAX multipurpose vehicle (MPV). In addition to inherent energy-absorbing properties for enhanced safety, XENOY iQ resin reduces impact on the environment and helps Ford lower the overall carbon footprint of the C-MAX vehicle. The resin – upcycled from up to 60 percent post-consumer plastic waste – not only relieves the burden on landfills, but also reduces the amount of hydrocarbon-based fuels needed in the production process. In fact, the XENOY iQ resin manufacturing process consumes 55 to 75 percent less fossil fuel than other engineering thermoplastics in the marketplace today and reduces CO2 emissions by a comparable amount. Most recently, XENOY iQ resin has been used on upper load path energy absorber of Jaguar Land Rover’s Evoque.
Also on display is a prototype all-plastic steering wheel. A traditional steering wheel is made up of a die-cast magnesium or an aluminum armature overmoulded with flexible urethane foam. Using injection moulding to process an advanced material such as LEXAN EXL PC copolymer resin offers a fresh approach to this part’s design, allowing for reduced weight and mass, added space for electronic components and greater design freedom for enhanced styling and innovative aesthetics. Injection moulding, compared to die-casting and finishing, also allows automakers to avoid secondary operations and streamline production, while reducing greenhouse gas emissions from the manufacturing process.
SABIC® PP PHC27, used in automotive applications reinforced with long glass fibers, will be run by ARBURG GmbH + Co KG on their stand 3101 in Hall A3.
Customer Solutions for Appliances
SABIC’s Innovative Plastics offers OEMs and tiers a first-class portfolio of innovative materials for appliance applications, which meet regulatory requirements and standards, and provide enhanced aesthetics. In line with growing demand for component miniaturization, moulding with increasingly thinner walls and ever more complex parts.
For example, the range of CYCOLOY™ resins with both flame retardant and non-flame retardant properties offer tailor-made material solutions for typical internal and external parts of appliances. These resins are typically used by our customers for washing machines, dryers and microwave ovens.
The incorporation of post-consumer recycle (PCR) materials is an important component of SABIC’s sustainability strategy and another example of the company’s proactive approach to changing customer needs. Up-cycling, which is a chemical vs. a mechanical process, extracts the feedstock in its pure form, helping to ensure the high performance of materials containing PCR content. Award-winning VALOX iQ™ resin is based on polybutylene terephthalate (PBT) that uses post- consumer polyethylene terephthalate (PET) feedstock. It is upcycled into a new engineering plastic for typical electronics, household appliances and automotive applications, converting waste from a product whose life was measured in weeks, into an engineering resin for durable products with lifetime measured in years. VALOX iQ resin helps to divert waste from landfills, and provides up to a 49 percent reduction in both CO2 emissions and process energy utilization per kilogram of PBT.
Customer Solutions for Packaging with SABIC® PP Qrystal and SABIC® PP Flowpact
Converters in the packaging industry benefit from new levels of optical performance in their products thanks to the SABIC® PP Qrystal range while making energy savings during production when using both SABIC® PP Qrystal and SABIC® PP Flowpact grade families. Foremost is the ability to make cost savings in unit production costs (up to 15%) and energy savings through lower cycle times, with further additional benefits for related environmental considerations.
Both grade families are part of SABIC polypropylene portfolio’s policy of creating high added value products that work alongside the core bulk materials. The idea is to create a broader range of high-performance products that meet specific needs, opening up the possibility of one-stop shopping for our PP packaging customers, globally.
Visitors will be able to see SABIC® PP FPC 55 running on an injection moulding machine at the stand of Swiss-based company Netstal-Maschinen AG - stand 7304, Hall A7. Stork Plastics Machinery B.V., based in the Netherlands, will be running SABIC® PP FPC100 on one of their machines - stand 7202, Hall A7.
Customer Solutions for Healthcare
Customers at Fakuma 2012 visiting SABIC’s stand, will be able to see an example displayed of SABIC® HDPE PCG4906, a new grade of high density polyethylene (HDPE) intended to meet the demands typically required of large containers such as IBCs, open & tight head drums and jerry cans used in healthcare applications. It is a high purity resin that meets European and the American pharmacopeia requirements. SABIC has cooperated with Mauser, a well-known supplier of blow moulded industrial packaging solutions, to ensure that the product has the right balance of density, melt flow, impact strength and environmental stress crack resistance, furthermore, it has the physical and mechanical properties typically required for the production of containers with volumes up to 1.000 litres, which comply to UN regulations for the transportation of dangerous goods.
SABIC will also display a healthcare application - PWB Health Ltd.'s Breastlight, a home-use device that makes it easier for women to perform self-breast examinations by shining a light on breast tissue to illuminate internal changes. To optimize the performance and durability of the Breastlight, LEXAN and CYCOLOY healthcare resins are used in the housing and lens of the device.
Customer Solutions for LED & Lighting
SABIC’s Innovative Plastics business is displaying the vast scope, versatility and quality of its material technologies for typical lighting applications, including the LEXAN LUX family of high-performance polycarbonate (PC) resins for light emitting diode (LED) lighting, and other specialty compounds for the lighting industry. SABIC’s LEXAN LUX flame-retardant (FR) resins, featuring non-brominated, non-chlorinated technology, offer a choice of customizable diffusion levels or transparency and good luminance for lenses, diffusers and optics. Non-FR LEXAN LUX grades are typically designed for manufacturing optical parts requiring easy flow properties combined with very high light transmission and colour stability. They are typically suited for automotive and non-automotive lighting applications such as light guides and lenses. The entire LEXAN LUX series offers optimized optical and heat aging properties for LEDs with a wavelength of approximately 400 nanometers.
Also highlighted at SABIC’s booth will be LEXAN FXD polycarbonate (PC) resin used on the diffuser cover of the Fonckel B.V.’s Fonckel One Lamp. SABIC’s Colour Innovation Centre played a major role in the development of the Fonckel One diffuser cover. The facility in Bergen op Zoom, whose staff comprises more than 30 years of expertise in colour and effects technology, also offers more than 18,000 different colour and effect choices.
In addition, the company is presenting KONDUIT™ conductive compound for thermal management, in LED heat sinks. This specialty compound offers greater design freedom than traditional approaches.
High performance solutions with ULTEM™ materials
SABIC is spotlighting a variety of lightweight, high-performance composites and other advanced materials that are making important contributions to its customers’ sustainability initiatives across major global industries. In particular, the outstanding weight-out and non-halogenated flame retardance provided by SABIC’s high-performance ULTEM resin, a polyetherimide (PEI) material, is increasing its appeal as an environmentally responsible solution. SABIC will display ULTEM materials in foam, fiber, granulates for injection moulding and in Carbon fiber. Customers are choosing ULTEM materials for a broad range of applications – not just in Aerospace, where they have achieved notable successes, but also in Healthcare, transportation and building & construction.
Reader enquiries
SABIC
WTC Tower Ten Strawinskylaan 1475
1077 XX Amsterdam
Netherlands
SABIC
WTC Tower Ten Strawinskylaan 1475
1077 XX Amsterdam
Netherlands
Notes for editors
• Brands marked with ™ are trademarks of SABIC
• SABIC is a registered trademark of SABIC Holding Europe B.V.
• High-resolution photos are available upon request
About SABIC
Saudi Basic Industries Corporation (SABIC) ranks among the world’s top petrochemical companies. The company is among the world’s market leaders in the production of polyethylene, polypropylene and other advanced thermoplastics, glycols, methanol and fertilizers.
SABIC recorded a net profit of SR 29.24 billion (US$ 7.80 billion) in 2011. Sales revenues for 2011 totaled SR 189.90 billion (US$ 50.64 billion). Total assets stood at SR 332.78 billion (US$ 88.74 billion) at the end of 2011.
SABIC’s businesses are grouped into Chemicals, Polymers, Performance Chemicals, Fertilizers, Metals and Innovative Plastics. SABIC has significant research resources with 16 dedicated Technology & Innovation facilities in Saudi Arabia, the USA, the Netherlands, Spain, Japan, India and South Korea. The company operates in more than 40 countries across the world with around 40,000 employees worldwide.
SABIC manufactures on a global scale in Saudi Arabia, the Americas, Europe and Asia Pacific.
Headquartered in Riyadh, SABIC was founded in 1976 when the Saudi Arabian Government decided to use the hydrocarbon gases associated with its oil production as the principal feedstock for production of chemicals, polymers and fertilizers. The Saudi Arabian Government owns 70 percent of SABIC shares with the remaining 30 percent held by private investors in Saudi Arabia and other Gulf Cooperation Council countries.
About Innovative Plastics
SABIC’s Innovative Plastics business is a leading, global supplier of engineering thermoplastics with an 80-year history of breakthrough solutions that solve its customers’ most pressing challenges. Today, Innovative Plastics is a multi-billion-dollar company with operations in more than 35 countries and approximately 9,000 employees worldwide. The company continues to lead the plastics industry with customer collaboration and continued investments in new polymer technologies, global application development, process technologies, and environmentally responsible solutions that serve diverse markets such as automotive, electronics, building & construction, transportation, and healthcare. The company’s extensive product portfolio includes thermoplastic resins, coatings, specialty compounds, film, and sheet. Innovative Plastics (www.sabic-ip.com) is a wholly owned subsidiary of Saudi Basic Industries Corporation (SABIC).
Related images
Editorial enquiries
Rachel Kundra
SABIC
Aline Stanworth
SABIC
Kevin Noels
Marketing Solutions NV