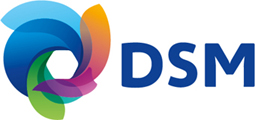
6 Mar 2007
HITACHI AUTOMOTIVE SYSTEMS EUROPE BENEFITS FROM FLOW, STRENGTH & DIMENSIONAL ACCURACY OF ARNITE® PBT
Hitachi Automotive Systems Europe, Ltd., has selected a reinforced Arnite® polybutylene terephthalate (PBT) blend from DSM Engineering Plastics for injection moulded mass airflow sensor body destined for Audi engines. Arnite TV4 261 30% glass reinforced grade PBT provides a combination of properties important to the application, including excellent flow, long term dimensional stability, stiffness and strength over a wide temperature range and chemical resistance. Production requires only moulding – no annealing is required to relieve internal stresses that could lead to warpage.
"Throughput is excellent with this design," said Andrew Bridge, Procurement & Design Manager for Hitachi. "The ability to mould the unit in one piece without annealing saves us two production steps compared to less sophisticated, two-piece approaches with alternate materials."
The Hitachi body serves both to mount the mass airflow sensor system precisely and to shape air flow using a moulded-in grid. To control the turbulent airflow, the grid induces a laminar flow that helps ensure accurate feedback about engine air intake temperature to the engine control unit. Mass airflow sensor data help engine control systems maintain an optimum air-fuel balance.
The grid's thin-wall elements and intricate geometry benefit from Arnite's flow properties, minimising moulded-in stresses and strains that later might contribute to warpage or unpredictable dimensional change, causing the sensor to misread airflow.
The design process for the component was a collaboration involving Hitachi, moulder and toolmaker W.H. Smith & Sons, Ltd., materials and processing expert DSM Engineering Plastics and design and mold flow specialist DSM/DADC (Design and Development Centre).
Reader enquiries
DSM Engineering Materials
30 Pasir Panjang Road #13-31
Mapletree Business City
Singapore 117440
Singapore
Notes for editors
About Hitachi Europe Ltd.
Hitachi Europe Ltd., is a wholly owned subsidiary of Hitachi, Ltd., Japan. Headquartered in Maidenhead, UK, it has operations in 15 countries and employs 470 people across Europe, the Middle East and Africa. As a 'Best Solutions Partner' Hitachi Europe tailors its services and solutions to meet the specific needs of its customers. Hitachi Europe comprises eleven key business areas: power and industrial systems; rail; industrial components & equipment; information systems; high performance computing; digital media; display products; air-conditioning and refrigeration systems; procurement and sourcing; corporate technology group (research & development) and the Hitachi Design Centre. Hitachi Automotive Systems Europe Ltd. is headquartered in Horwich, Bolton U.K. For more information about Hitachi Europe Ltd., please visit http://www.hitachi-eu.com
DSM Engineering Plastics
DSM Engineering Plastics is a business group forming part of DSM's Performance Materials cluster. DSM Engineering Plastics is a global supplier of Stanyl® PA46 and Akulon® 6 and 66 polyamides, Arnitel® TPE-E, Arnite® PBT and PET polyesters, Xantar® polycarbonate, Yparex® extrudable adhesive resins, and Stamylan® UH Ultra High Molecular Weight PE. These materials are used in technical components for electrical appliances, electronic equipment and cars, in barrier packaging films as well as in many mechanical and extrusion applications. The business group had annual sales of EUR 705 million in 2005. With Stanyl®, it is the global market leader in high heat polyamides.
Akulon®, Arnite®, Arnitel®, Stanyl®, Stamylan® UH, Xantar® and Yparex® are registered trademarks of DSM Engineering Plastics.
Related images

Intricate Audi engine mass airflow sensor body for Hitachi Automotive Systems Ltd. is made from Arnite® TV4 261. The 30% glass fiber reinforced injection moulding PBT resin provides a combination of properties important to the application, including excellent flow, long term dimensional stability, stiffness and strength over a wide temperature range and chemical resistance.
Editorial enquiries
Sandra Coolen
DSM Engineering Materials
Nancy van Heesewijk
EMG